We had the pleasure of visiting the James Cropper paper mill in Cumbria, where many of our papers are made. Having made our own paper on a very small scale, so we had an understanding of the process. But to see the scale of it here was something quite different. The noise, the smells (and the mess) brought it to life.
The mill has been situated here since 1845, previously a cotton mill. It used to run on power from the river, and of course being a paper mill it still relies heavily on the running water that passes beside and beneath the factory.
The small town of Burneside near Kendal has been a major local employer for generations. As we arrived in the morning, we got chatting to a man who had worked ‘Machine number three’ for 40 years before retiring 10 years ago. And our cab driver back to the station told us his father-in-law and brother-in-law both worked at the paper mill.
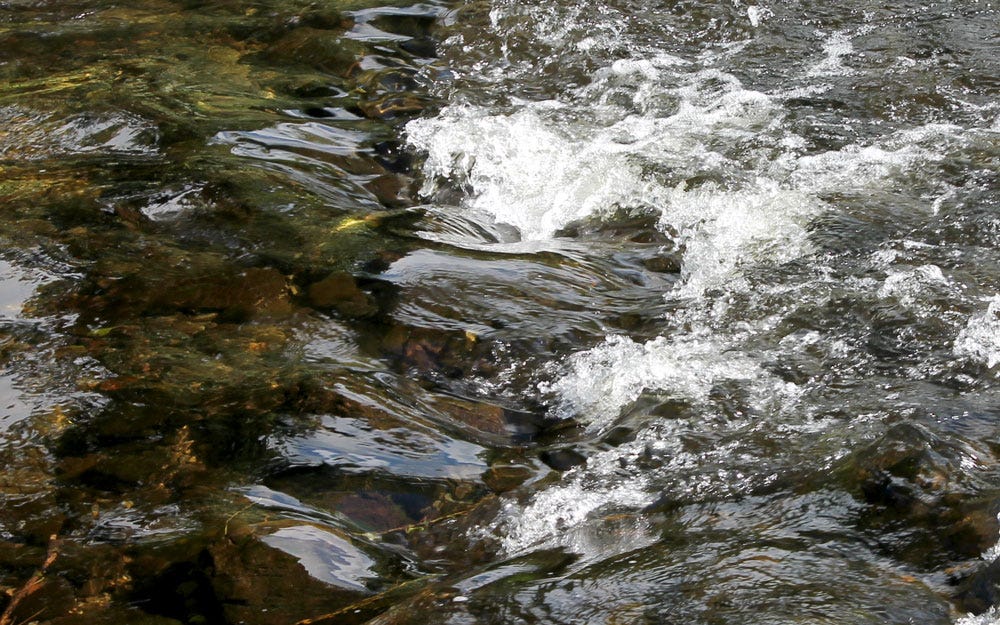
The River Kent provides the much needed mega-tonnes of water used in paper-making. The mill works closely with the Environment Agency to ensure that this water arrives crystal clear must be returned to the river either as clean, or cleaner, than when it left. The water is so clean that crayfish and fresh-water mussels live in it.
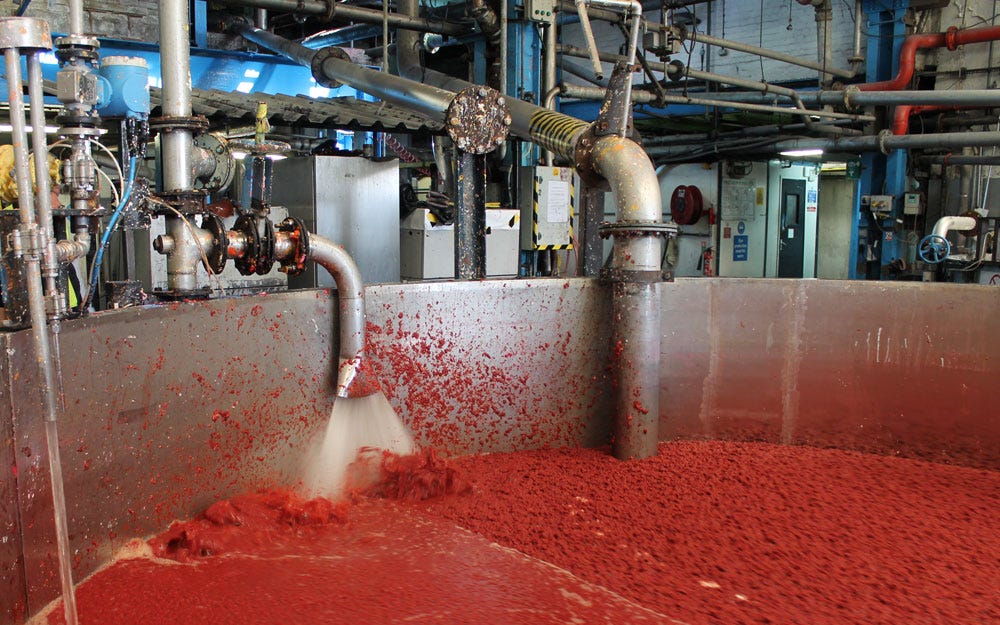
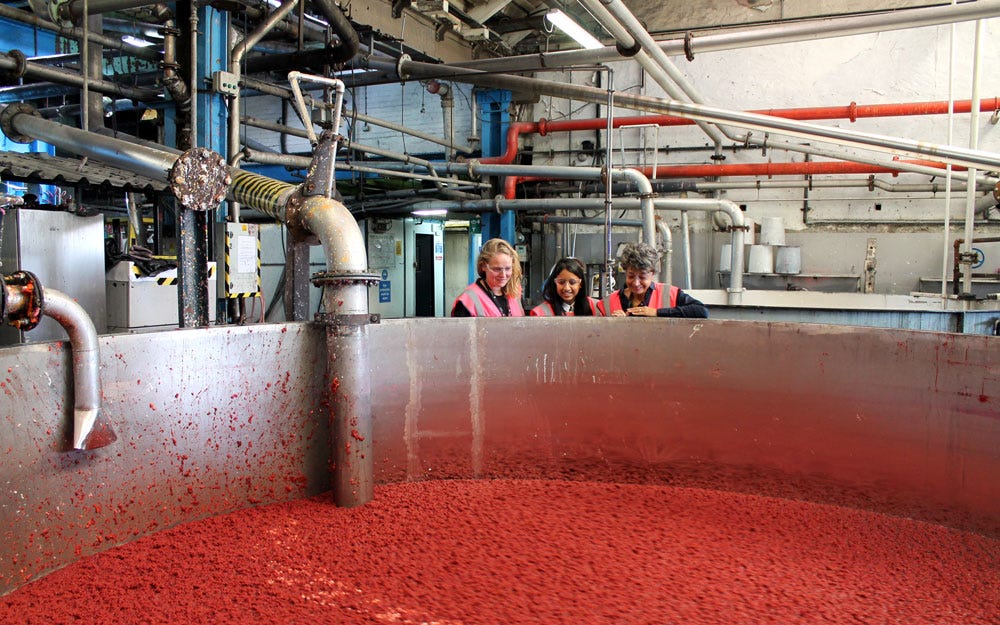
You only have to stand next to one of these giant vats for a few moments to see what all that water is needed for. We were delighted to see some really vivid colours in production on the day we visited.
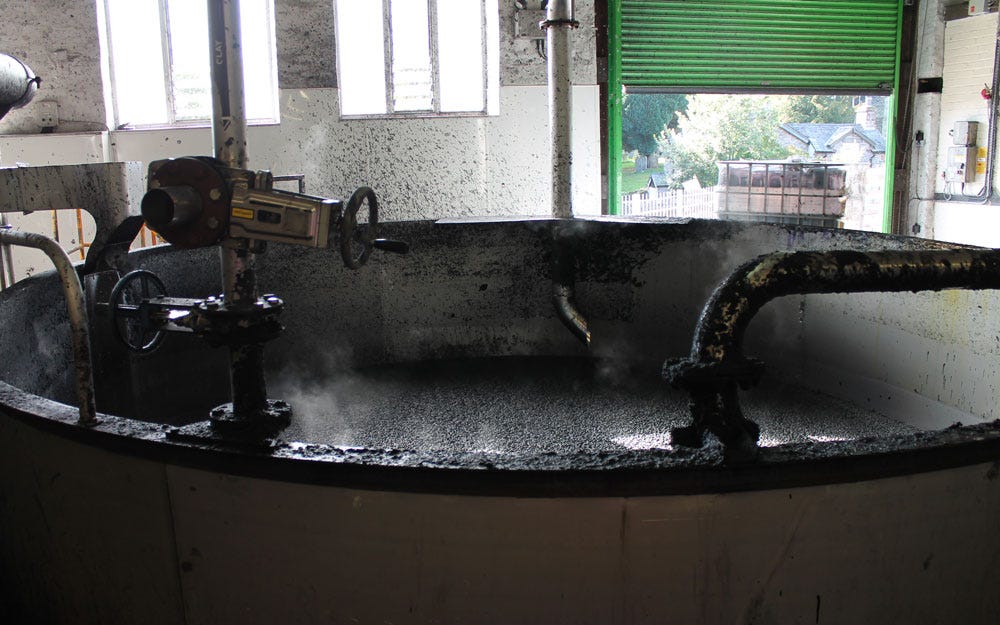
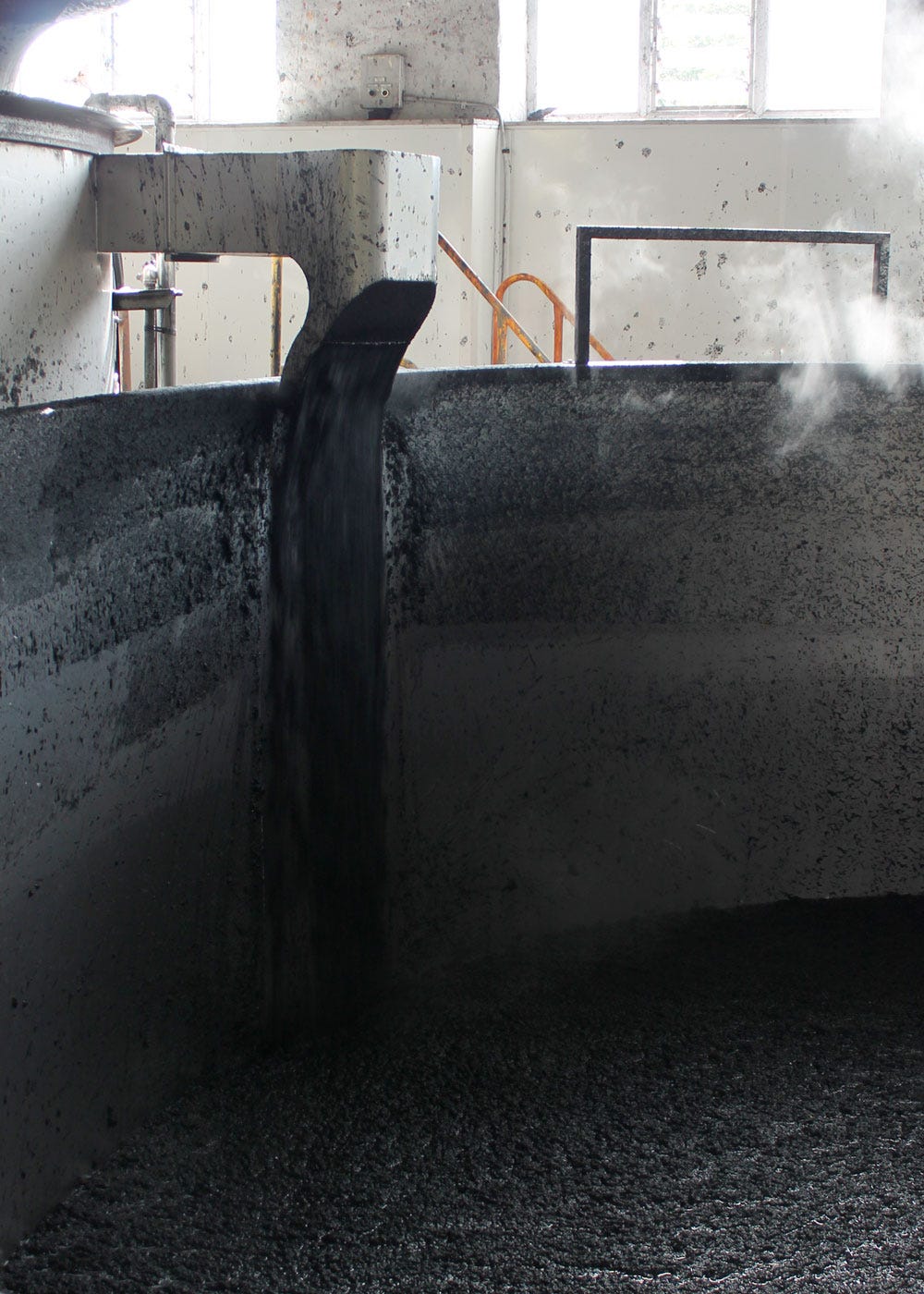
You can smell the moisture in the air, much of it rising as steam from the hot, sloppy pulp. The deep coloured dies are added at this stage to embed the colour in the sheet — this is why when you tear a sheet of good quality paper like Colorplan, the colour is consistent all the way through, rather than showing a white edge.
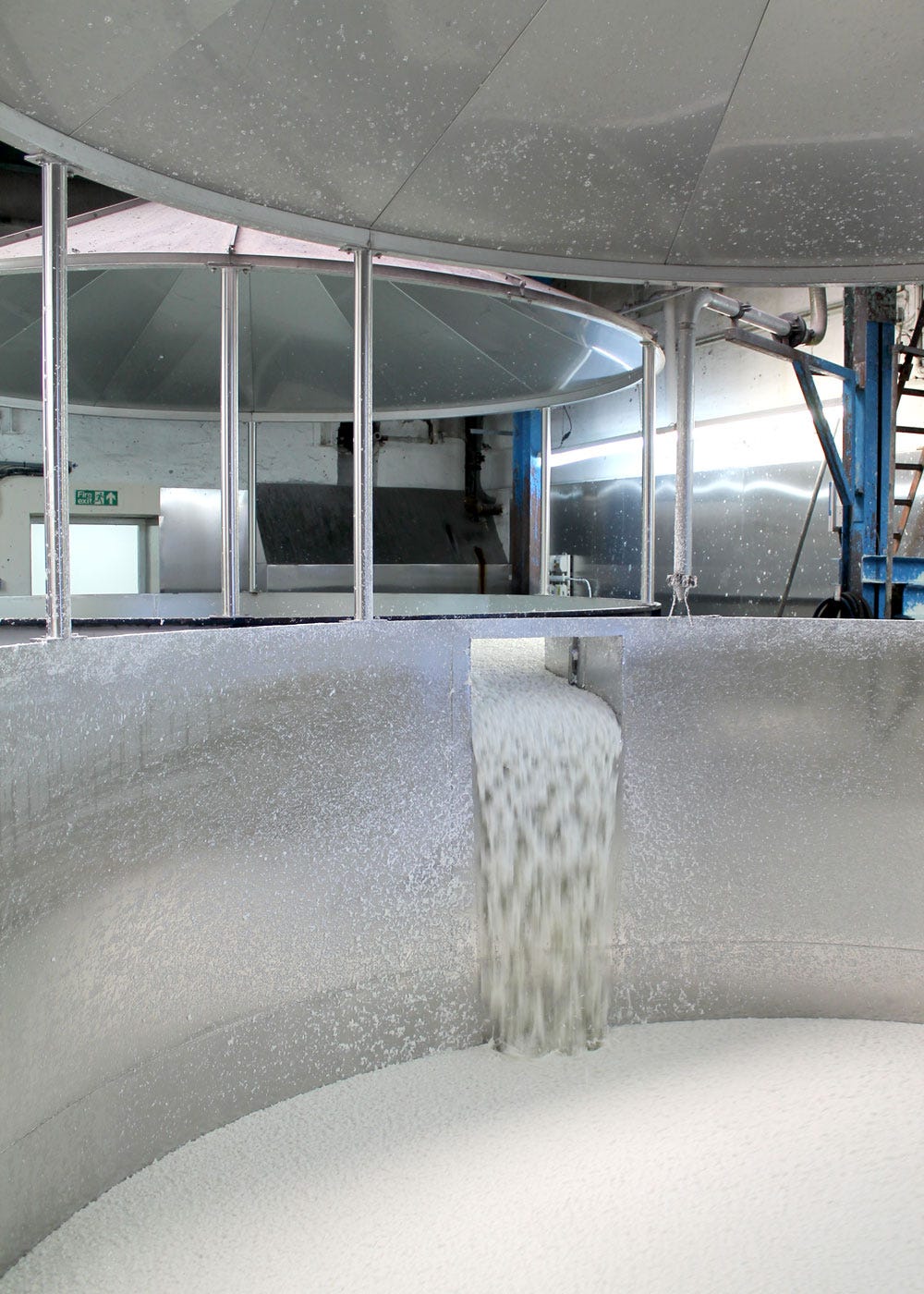
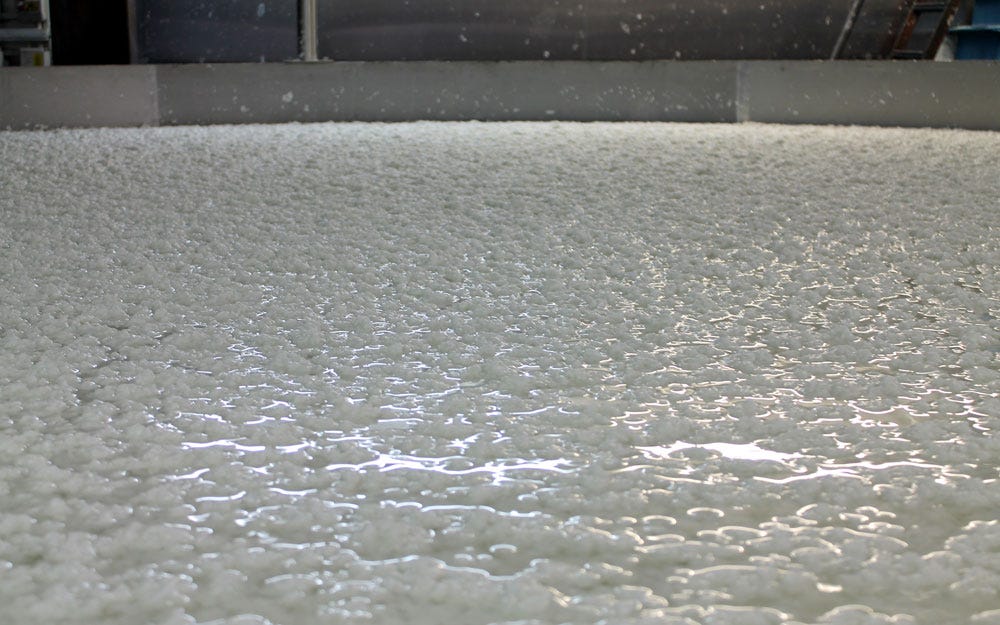
The pure whites were rather beautiful too. Just before this step, the pulp and water have been loaded up into a blender the size of a small house! Next they are churned and mixed to a homogenous pulp, before being transformed into beautiful sheets of paper.
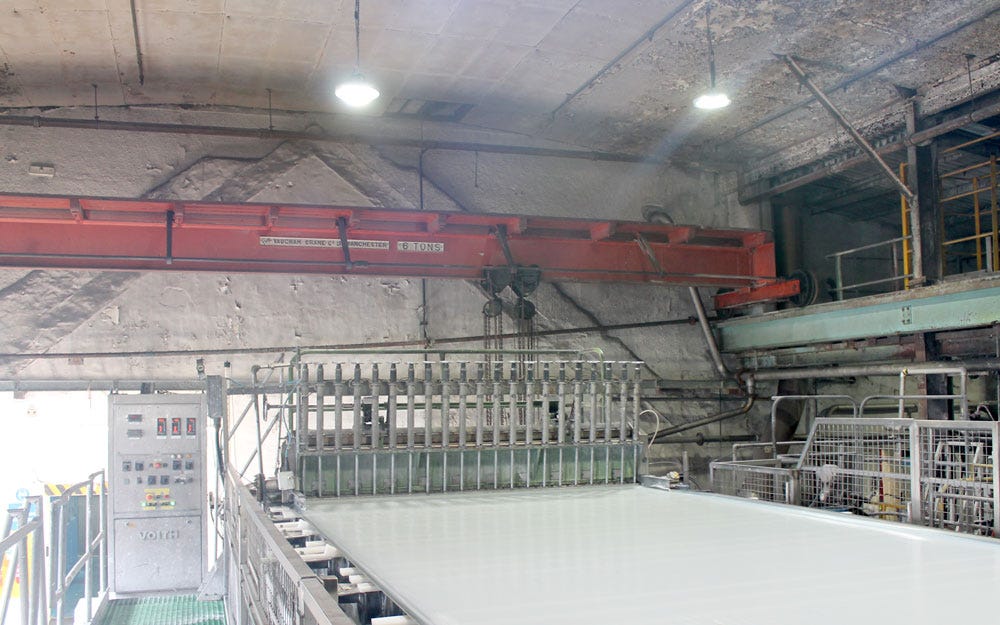
Here’s where they start to become something more recogniseable. The hot pulp is pumped out onto the wire mesh beneath. The faster it goes, the thinner the paper will be (lower gsm) and the slower it goes, the thicker the paper will be (higher gsm).
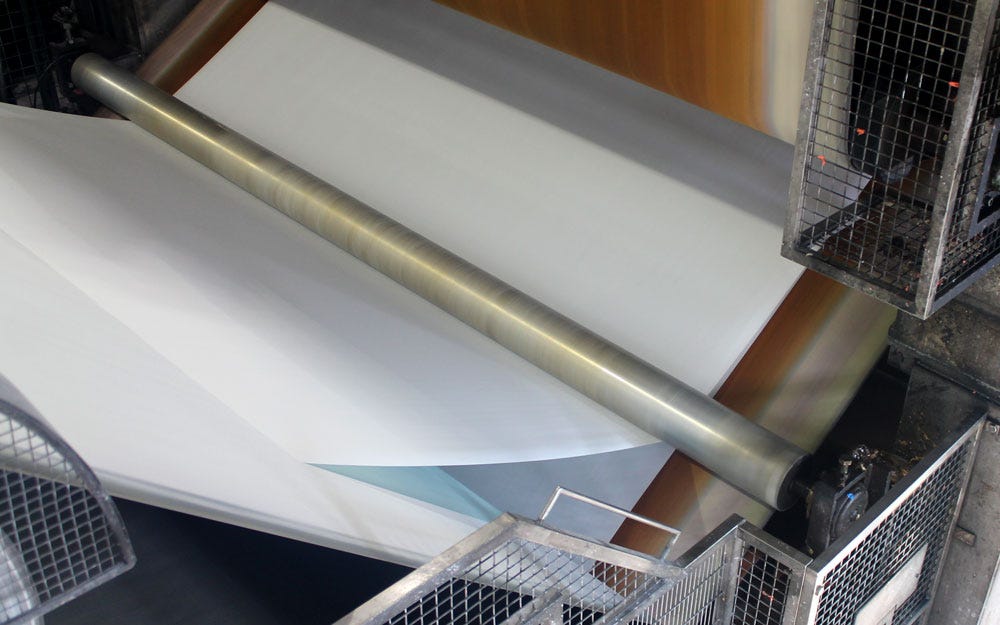
For many of our favourite papers, the next stage is the ‘twin wire.’ This is what gives our Notebook Mark One such beautiful smooth pages which are equally smooth on both sides. Unlike other papers which have a smoother ‘front’ and rougher ‘back’, in this process two sheets forged together with the smooth sides facing out, so that at the end of the process the sheet has a perfect surface on two sides.
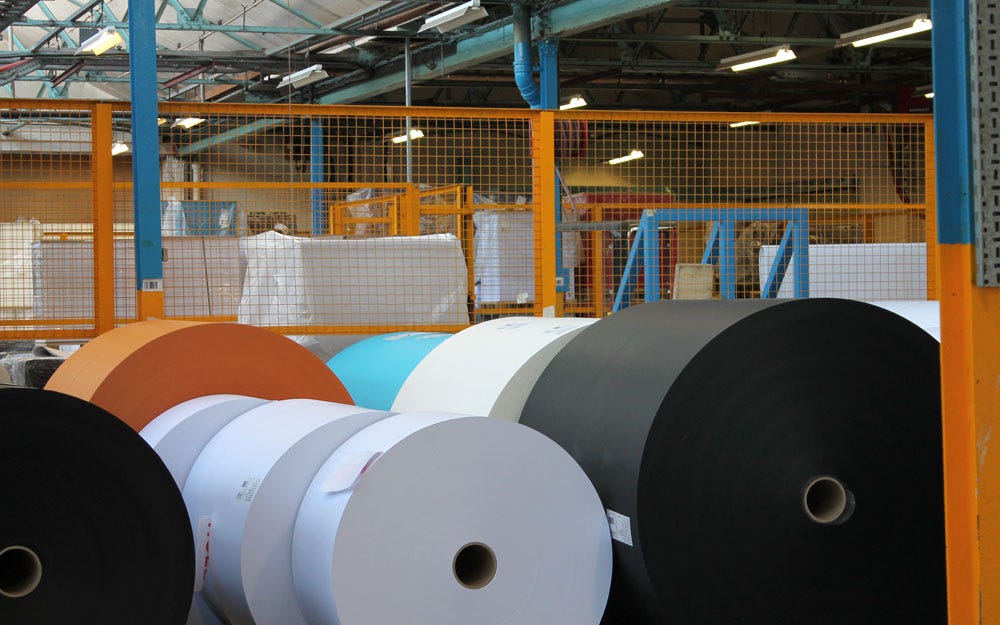
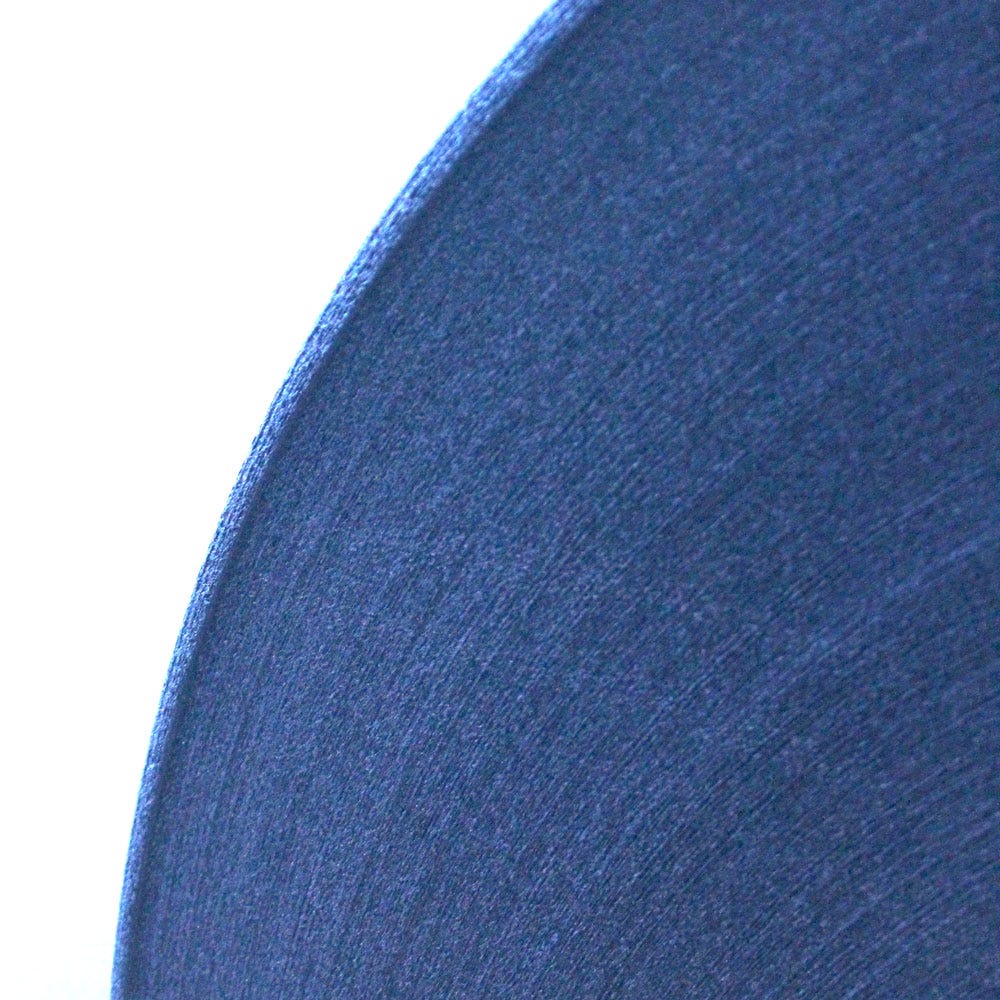
The paper is made into giant rolls of paper, before being cut into flat sheets.
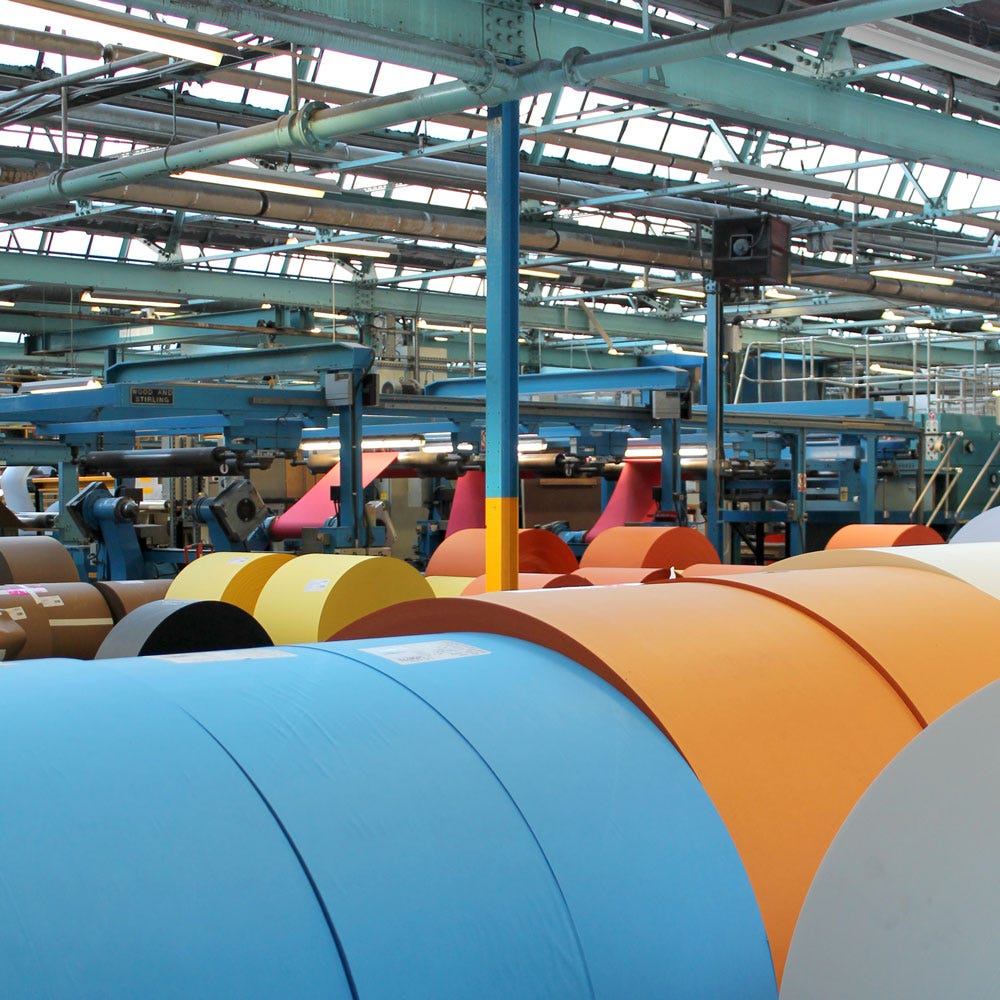
The flat sheets are stacked and counted for packing.
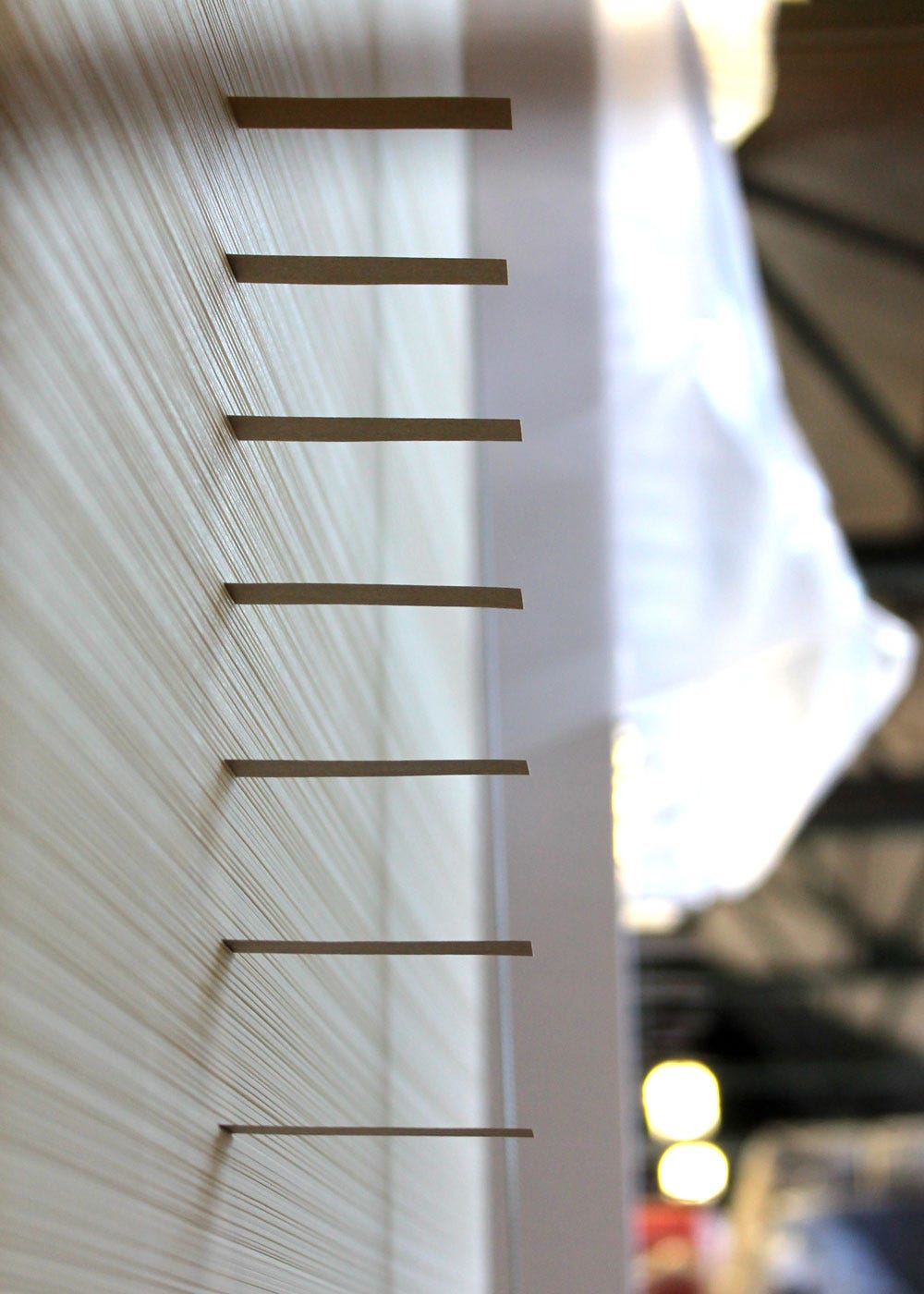
Thank you to James Cropper, and to G.F. Smith for organising our tour in September 2018. We were blown away by this process and the brilliant people behind it. The attention to detail and perfectionism is impressive to see, and we are so proud to work with these wonderful materials.